In this enlightening Q&A, Simon Blackham, Senior Technical Manager at Recticel Insulation looks at the implications of the new Part L (Conservation of Fuel and Power) requirements which in response to climate change, aim to reduce carbon emissions in new homes and non-residential buildings by 75% - 80% (compared to 2013 standards).
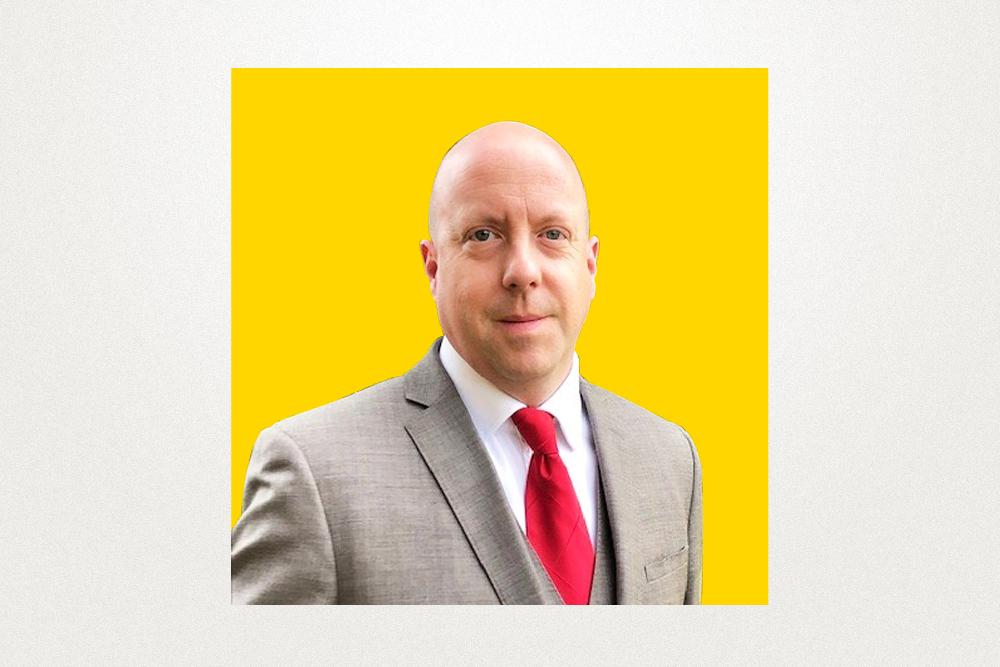
Q: The Part L changes detail a range of increases in thermal performance requirements. What are your thoughts as to whether a fabric-first approach to building remains the most direct route to achieving the government’s net-zero target?
A - Simon Blackham: For renewables such as heat pumps, a fabric-first approach is fundamental for them to work efficiently and provide the right level of comfort for occupants with the lower working flow temperatures provided. It’s also essential to futureproofing consumers and taxpayers against unnecessary future costs and disruption that could be required from a retrofit perspective if the fabric isn’t addressed during initial construction.
Q: The new regulations focus on adopting a fabric first approach to achieving as-designed building performance, and the benefits of this strategy have long been known. Has the construction industry been slow to acknowledge the need to prioritise the design of walls, floors and roofs in property construction? If so, why?
A - Simon Blackham: Although known, increases in insulation and to the fabric performance will essentially add cost to the build which is unlikely to be welcomed by the housebuilder. However, as stated, prioritising a building’s fabric in respect of design is a necessity for renewable technologies to function efficiently. Education is key to making consumers more aware of the importance of the fabric’s performance. Recent news reports, for example, have included extensive coverage of the global rise in fuel costs. This in turn should make it easier to sell the idea of better performing properties with slightly higher costs, as the long-term running costs will be significantly lower.
Q: What challenges will the Part L changes and the subsequent introduction of the Future Homes Standard pose to property builders?
A - Simon Blackham: As stated, with tighter targets there will be more insulation, potentially larger footprints or changes to materials. With the changes and requirement of imagery to improve the project monitoring process, it will hopefully mean better homes for consumers and as-built construction that reflects the plans. This should reduce building bad practice and improve junction detailing.
Q: What part does high-performance polyisocyanurate PIR play in creating the ideal thermal envelope and meeting the new Part L requirements?
A - Simon Blackham: PIR offers flexibility and greater options, enabling designs to be changed without substantially changing existing practices. PIR within lightweight blockwork is capable of achieving a 0.18 W/m2K U-value with a conventional 100mm masonry cavity construction (300mm wall + plasterboard on dabs). PIR is not a new material. It has been used safely for a number of decades, making it a tried-and-tested product for a wide range of applications.
Q: Why is PIR now seen as the go-to ‘fabric-first’ material and how does its performance compare to mineral fibre-based insulation?
A - Simon Blackham: PIR has a lower thermal conductivity and higher thermal resistance in comparison to mineral wool. This enables elemental details including PIR to be much thinner. Hence, PIR offers greater flexibility in terms of its application, as well as being more user-friendly for installers. The fact that it remains dimensionally stable and does not sag or slump also ensures long-term performance, as the PIR will remain where it’s required.
Q: Why is it important that specifiers consult with an insulation specialist prior to embarking on a fabric-first design for their property?
A - Simon Blackham: In the first instance, it’s recommended to consult an SAP or SBEM energy assessor to establish project-specific fabric targets. Using such procedures gives flexibility in design whilst maintaining compliance.
Depending on design, certain applications may not lend themselves to a particular type of insulation material. Therefore, it’s advisable to consult with a specialist to ensure that a specification meets the necessary requirements in relation to thermal performance, fire, acoustics, loading etc.
Q: The latest amendment to Part L of the Building Regulations is the biggest update to the standard since 2013. Do the amendments go far enough, or is it a case of too little, too late in relation to the changes boosting the UK’s net-zero ambitions?
A - Simon Blackham: It is a step in the right direction and as mentioned, is necessary to support the use and ensure the efficiency of low carbon technologies. A building’s fabric performance needs to be carefully examined and utilised to improve occupants’ comfort and wellbeing.
More education is required in relation to the Part L amendment, with additional governmental support being necessary to ensure the regulations’ effective implementation. The retrofit of existing building stock will also be vital in achieving such targets as net-zero. Therefore, a successful scheme that benefits consumers and occupiers without hitting them hard in the pocket needs to be created as soon as possible.
Q: What changes, if any, would you liked to have seen included as part of the recent Part L review?
A - Simon Blackham: It might have been an idea to look further into SAP or SBEM in relation to fabric targets. Such a process would help ensure that the entire building envelope performs as required. Moreover, the flexibility in relation to elements within the procedural mix (SAP, SBEM) would help alleviate impact efficiencies of technologies and comfort.
Q: In terms of fabric-first construction how does the UK compare to Europe, where the approach appears more established?
A - Simon Blackham: In Europe, there is greater emphasis on education in relation to fabric-first construction, as well as government target setting. Ultimately, builders will look for the most cost-effective solution that still achieves the regulatory targets set by the government, so the design and constructions will always reflect this.
Q: As a leading PIR manufacturer, does Recticel’s customer service offering extend beyond supplying the required insulation grade and volume?
A - Simon Blackham: We can be consulted from an early stage to give advice on questions relating to material selection, installation, U-value targets and condensation risk analysis. Our technical experts are also available to offer guidance throughout the construction phases of a project to ensure a successful outcome. A range of helpful documentation is available via our website: www.recticel.com to assist with the insulation design, specification and installation process. A free-of-charge U-value calculator that allows users to assess their building’s elemental thermal performance is also available via the website. This is supported by our comprehensive CPD offer, and essential data regarding the properties and performance of our industry-leading PIR insulation products.
Use our U-Value Calculator
For your Part L Requirements, use our free-to-use U-Value Calculator to assess your building's elemental thermal performance.