End of life: closing the loop
🡄 Go to sustainability overview
Waste management and recycling account for 25% of our carbon emissions. Next to raw materials, they’re the second most important contributor to our PIR insulation boards’ footprint. That’s why our entire sustainability strategy is focused on closing the loop and recycling our waste into high-quality and high-value raw materials. And that’s precisely our main challenge: to maintain the high quality and properties of the recycled materials.
There’s roughly 2 processes to recycle PIR insulation – through mechanical recycling or chemical recycling.
Chemolysis: our gateway to circular insulation
Mechanical recycling involves mechanical processes such as grinding, washing, separating, drying, re-granulating, and compounding. The result is recycled pellets, which can be used to make new products. The only problem with PIR insulation is that the outcome of the recycling processes, the pellets, are of a lower quality than the original material. As the core of our insulation boards is sandwiched between two multilayer facings, they end up contaminating the recycled foam. While the pellets can be used for the production of lower-value products like insulating screed, they can no longer be recycled into new, high-quality PIR insulation boards.
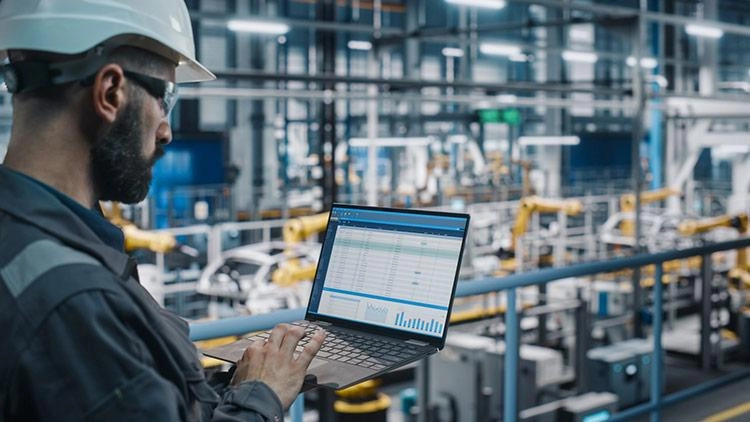
Mechanical recycling
Mechanical recycling involves mechanical processes such as grinding, washing, separating, drying, re-granulating, and compounding. The result is recycled pellets, which can be used to make new products. The only problem with PIR insulation is that the outcome of the recycling processes, the pellets, are of a lower quality than the original material. As the core of our insulation boards is sandwiched between two multilayer facings, they end up contaminating the recycled foam. While the pellets can be used for the production of lower-value products like insulating screed, they can no longer be recycled into new, high-quality PIR insulation boards.
Chemical recycling
Chemical recycling involves the transformation of the PU polymer chain. When chemolysis is used to depolymerize the PU, the molecules are broken down into smaller building blocks, which may then be reassembled into its original high-quality raw materials like MDI and polyol. You could say they reverse the production process. It is the only truly circular solution to recycle PIR foam. The challenge here is to optimize the yield of the chemolysis process in terms of purity and quality of the recycled molecules, hereby dealing with all kinds of contamination.
Projects
We’re currently investing and collaborating in a project that has the potential to revolutionize insulation by developing a recycling process for PIR insulation that can be repeated over and over again.
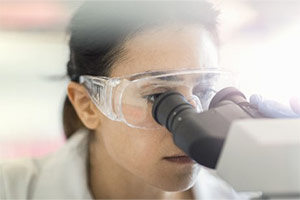
Chemical rigid foam recycling
With Recticel Insulation, we want to reassess the end-of-life management of our rigid PIR foam and find a way to reuse it in new insulation of the same quality and performance as the original board. In fact, we’re exploring an innovative way to close the loop on our foams, and we’re doing it through chemolysis.
Read more about chemical recycling